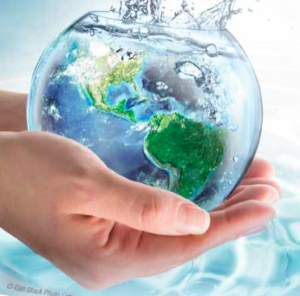
Ontario Regulation 20/17 “Ontario’s Large Building Energy and Water Reporting and Benchmarking (EWRB) Requirement,” made under the Green Energy Act stipulates energy and water monitoring guidelines for most 50,000-square-foot or larger commercial office buildings, hospitals, K-12 schools, medical offices, senior care communities and residential care facilities, supermarkets, food stores, and other building types with some criteria for exemption.
The program doesn’t directly reference or recommend specific energy-saving measures; however, it points to an excellent set of talking points for contractors, manufacturers, and anyone else representing the mechanical insulation industry.
Under Ontario’s program, building owners will use the free ENERGY STAR Portfolio Manager software to upload, manage, and compare buildings’ energy and water use. The information collected is used to give building owners perspective and an ongoing, real-time look at energy and water use; provide measurable benchmarks for improving efficiency; contribute to a more robust central database for the Environmental Protection Agency (EPA), used in the US and Canada; and, lend measurable date for future energy code development.
Development of such benchmarking initiatives assists building owners in managing energy use and cost using measurable goals and by evaluating results via comparison with similar facilities. Over time, the improvements can be measured and the value of energy efficient and water efficient buildings will shift accordingly.
“Disclosure of building performance information can motivate building owners to compete with one another and strive to improve their building performance year over year,” said the Ontario Ministry of Energy’s EWRB material. “It can also allow property and financial markets to compare building performance and value efficient buildings, enabling market forces that can drive efficiency investment.”
Building owners in Ontario are legally responsible for compliance under the new regulation and in the case of condominiums, the condo corporation is legally responsible. Non-compliance penalty information is still under development.
The prevalence of benchmarking is growing in Canada, especially since US buildings using ENERGY STAR Portfolio Manager have, on average, reduced energy consumption by seven percent over three years. So far, CivicAction launched a Race to Reduce challenge. Support from Building Owners and Managers Association, Canada Green Building Council (CaGBC), Real Property Association of Canada, and City of Toronto work along side Ontario’s initiative to further momentum.
The province of Manitoba currently offers building owners voluntary access to ENERGY STAR Portfolio Manager as a method of determining and measuring building performance, and providing the EPA information for comparative use against similar buildings.
Manitoba also launched its Race to Reduce last year, a four-year challenge aimed at reducing energy use in participating buildings by 10 percent. Modelled after the highly successful Race to Reduce run by CivicAction in the Greater Toronto Area between 2011 and 2015, Manitoba’s initiative hopes to meet or exceed the GTA’s campaign results, which involved more than 42 percent of the region’s commercial office sector helping to surpass the Race’s savings goal and achieve collective energy savings of 12.1 percent.
In 2011, the City of Vancouver set a green building target of a 20 percent reduction in energy consumption and greenhouse gas emissions from existing buildings by 2020 over 2007 levels. Energy retrofits to buildings are fundamental to the City achieving this goal, and are expected to reduce nearly a quarter of city-wide greenhouse gas emissions, or 160,000 tonnes of greenhouse gas emissions, according to the City’s Greenest City Action Plan.
In 2014, the Resolution B94 “Benchmarking Tools for Building Energy Use” was endorsed at that year’s Union of BC Municipalities (UBCM) Convention in Whistler, BC. At the 2017 event, the Ministry of Energy, Mines, and Petroleum Resources endorsed amendments to the Vancouver Charter to empower the City to require annual reporting of building energy use data for the purpose of benchmarking energy performance.
According to the CaGBC’s material, the organization has long supported energy benchmarking as a catalyst for energy-saving initiatives, and includes ENERGY STAR scores in its LEED certification criteria for eligible building types.
“Last spring, CaGBC released a white paper presenting a proposed national framework, based on industry and stakeholder consultations, to support the development of benchmarking policies throughout the country,” said the organization.
“There is a connection between saving water and inadequately and uninsulated hot water piping,” said Steve Clayman, director of energy initiatives for TIAC. “This is backed by discussions I have had with mechanical engineers on how heat loss in piping wastes water, and by a study conducted by the American Society of Plumbing Engineers that measured acceptable limits on how long it should take water to come up to a comfortable skin temperature.”
The American Society of Plumbing Engineers completed design considerations for hot water plumbing in its 2003 Domestic Hot Water Heating Design Manual that stipulate a 10 second or less wait for hot water acceptable, an 11 to 30-second wait marginal, and a 31-second or higher wait unacceptable.
The same group specifies in chapter 7 of its Plumbing Engineering Design Handbook Fundamentals of Plumbing Engineeering, “reducing fixture flow rates” and “applying economical thermal insulation” as mitigation measures.
“With Ontario’s regulations on wasted water coming into play, it’s time for the mechanical insulation industry to start having this discussion with everyone challenged with reducing water consumption,” said Clayman. “NECB-2015 and ASHRAE 90.1-2010 cover off the minimum pipe insulation thicknesses necessary.”