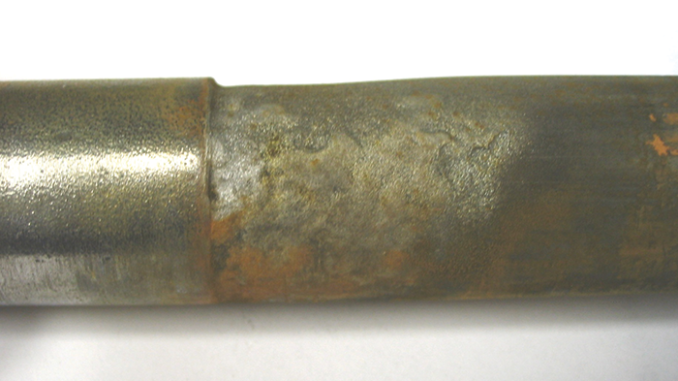
By / Monica Chauviere
“If the jacketing on the insulation is not damaged and nasty-looking for hundreds of feet of piping or on an entire large vessel, like a tower, there is not likely CUI on the steel.”
Wrong! This is a serious myth.
There is a high risk of corrosion under insulation (CUI) under hot service insulation if it is an absorbent type of insulation and if any of the following is also true:
- The insulation was installed before a coating of the proper technology to resist hot/boiling water was correctly installed (i.e., prior to approximately 1990).
- Third-party inspection by a certified inspector did not oversee the installation of a coating system that is suitable for hot water exposure, and the insulation has been there for more than 10–15 years.
- The hot service equipment is severely cyclic with elevated temperatures that swing regularly back down to ambient.
This is not to say that the myth does not apply to cold service insulation. In fact, it is equally true of cold insulation in services where the operating temperature is continuously or routinely above freezing. But for this discussion, we will focus on hot insulation.
Water, Water…
How does water get into the insulation system if the weather jacketing is not visibly damaged or missing? And, more importantly, how long does the water stay there? Industry experts seem to agree, and I’ve stated it many times: “It’s not a matter of if water will get in, it’s a matter of when.”
Let’s look at some of the less-obvious means of water entry that aren’t necessarily noticeable from a distance:
- Lack of caulk: Caulk (or the lack of it) is not often easy to see from even a few feet away. Oftentimes, protrusions and joints in an insulation system, which should be sealed with silicone caulk, are not accessible for true visual inspection. Even when caulk is there, it may not be adhered. I’ve seen a continuous, full fillet of caulk around a protrusion through the insulation, which had totally disbonded from the jacketing. It still adhered to the pipe, but was elevated about 1/8” above the jacketing. Obviously applied to a contaminated surface, this defect was found only by very close visual inspection with some probing.
- Caulk where it’s not supposed to be: It may sound odd, but sometimes caulk is a bad thing. Once water does get in, we want it to drain out quickly. When caulk is used to seal bottom terminations on vertical piping—or around nozzles at or near the six o’clock position on horizontal vessels—that’s a bad thing. Sealing such areas with caulk holds the water in, increasing the risk of corrosion and a host of other issues outside the scope of this article.
- Improperly oriented or designed protrusions: Especially when structural members are poorly designed, water can cup and funnel through the jacketing, directly into the insulation. From a distance, it doesn’t look like anything is wrong with the condition of the insulation. But just an inch or so of missing caulk at one of these key locations can funnel in large volumes of water.
- Intermittent or cyclic operation: When steel cools slowly to ambient temperature, water vapor is drawn to the surface and condenses there. If the mode of operation includes cooling to ambient or near-ambient temperature, and this occurs repeatedly, it means that water is coming into the insulation system. If this cycle occurs often enough, the wet/dry impact can exacerbate corrosion at any defect, even with a proper coating system.
Unfortunately, the water entry problem isn’t constrained to only water-absorbent insulation. Some facilities have employed insulation materials for hot service, which were historically relegated to cold service applications.
These cellular structure foam materials of both rigid and flexible nature have some serious drawbacks when it comes to use in hot service. One of the drawbacks is that such insulation materials were not designed to “breathe,” nor do they easily release the water that may be trapped behind the insulation, or the water vapor created when the water is vaporized by the heat of the process.
New Innovations in Detecting CUI
There are a number of technologies and devices being tried today to help defray the high cost of finding CUI.
Ultrasonic technology that can “see through” insulation to examine steel surfaces and detect mass loss of steel is one such method. This is still relatively new. Because failing to detect CUI can have catastrophic consequences, facilities are not yet convinced that this method is 100 percent reliable. Thought it’s time-intensive, many operators are staying on the conservative side and continuing to remove a minimum percentage of the insulation for visual inspection.
Another device inserts into and protrudes from the insulation system and activates a signal and light when it detects the presence of water. There is no indication whether corrosion is occurring, only that water is present. I don’t think there is a way to switch off the light or reset the device. I would imagine that this could be useful in a very specific situation and in a special location that would be easily accessible; otherwise, it would seem that accessing and checking these activated devices would be cost-prohibitive.
The Proper Mindset to Detecting Corrosion Under Insulation (CUI)
It would be a wonderful thing to know where corrosion was occurring. But since we don’t have that luxury, we need to rely on knowledge gained from our past mistakes and use our God-given logic and common sense.
The logic goes something like this:
- Traditional insulation materials, which exist on almost all facilities today, are a rigid type of insulation.
- This means that there is a small, yet real annular space behind that rigid insulation into which water can travel.
- The vast majority of these facilities were built with, and are still today primarily covered with, water-absorbent insulation and with design details that hold up water and prevent prompt drainage.
- Insulation can and does enter insulation systems that do not have the appearance of being damaged.
Knowing particular operating and equipment design details; recognizing key aspects of the operating environment and the type and age of the insulation; and understanding what details to look for in the field can give us a fairly good start at knowing where to begin the search effort.
There is no crystal ball, but with key information and expertise, time and money can be saved in the discovery process.
Takeaway: Knowing particular operating and equipment design details; recognizing key aspects of the operating environment and the type and age of the insulation; and understnading what details to look for in the field—these will help us to find out where corrosion occurs.
Monica Chauviere is a recognized expert in the field of corrosion under insulation (CUI), with more than 30 years’ work with ExxonMobil Baytown Refinery and ExxonMobil Research and Engineering Company.
This article originally appeared at corrosionpedia.com/cui-myth-4-theres-no-cui-if-the-jacketing-isnt-damaged/2/2018 in 2015. It was updated in 2018 and reviewed in 2021. It has been reprinted with permission from the author and corrosionpedia.com▪